Temperature Measurement Molten Casting: Mastering Aluminum Melting & Infrared Monitoring
Temperature Measurement Molten Casting is a critical component of modern aluminum melting and casting operations. In this comprehensive guide, we explore precise techniques and instrumentation for monitoring temperature during the transition from solid to molten states and throughout the casting process. Accurate thermal control ensures metal purity, enhances process stability, and optimizes energy efficiency. Drawing from real-world applications and expert insights, this guide focuses on best practices for using infrared pyrometers in industrial aluminum foundries.
Table of Contents
Why Temperature Measurement in Aluminum Melting & Casting Matters
Aluminum casting is sensitive to even small temperature fluctuations. Overheating can degrade metal quality, increase dross formation, and waste energy, while underheating may result in incomplete mold filling or structural weaknesses. Real-time temperature control ensures:
- Consistent alloy quality
- Reduced scrap and rework
- Optimized energy consumption
- Safer working conditions
Infrared pyrometers offer the non-contact precision required in these harsh, high-temperature environments.
Key Applications & Pyrometer Configuration
- Dual Calibration for Solid and Molten Aluminum
The pyrometer operates using two dedicated calibration setups stored in the instrument’s memory:
Setup #1: for the solid state (stored in Group 1)
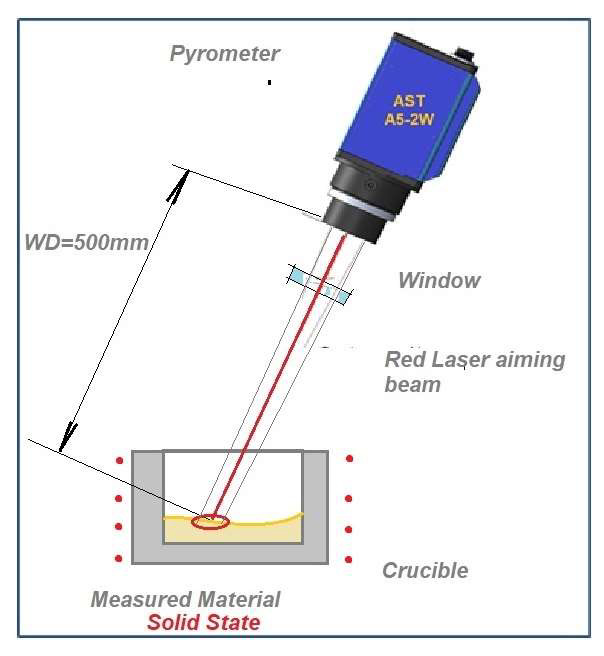
Setup #2: for molten metal (stored in Group 2)
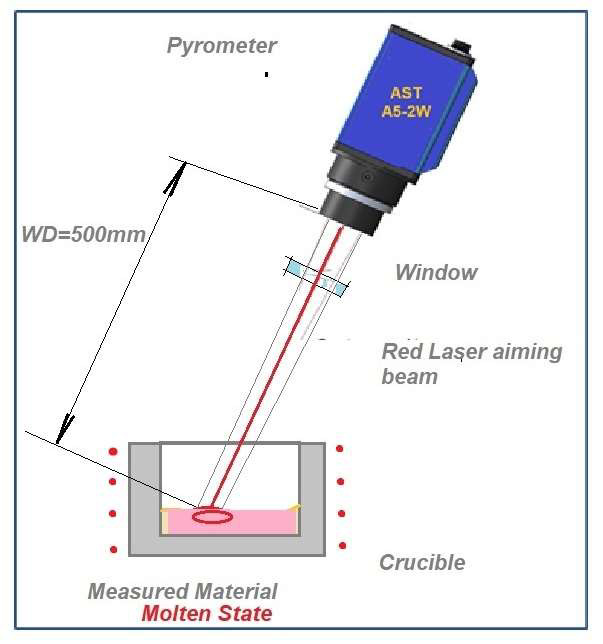

Recommended model:
A5-EX pyrometer
This device is capable of accurate readings as low as 200 °C on highly reflective surfaces like molten aluminum (ε = 0.04–0.05).
Each material state requires a unique emissivity calibration and memory group setup. Switching between groups must be clearly defined—whether by process automation, operator input, or signal triggers.
- Real-Time Monitoring of Moving Ingots
Use Case: Temperature measurement during ingot casting Molten aluminum is poured into molds on a slow-moving conveyor (< 0.5 m/s).
Key measurement formula:
- Observation Time = Width (d) / Speed (V)
Set the pyrometer’s reaction time to 50–70% of this window to average out cooling loss during transit.
- Recommended model: A5-IN
This setup ensures an accurate average temperature of the ingot across its visible cross-section as it moves past the pyrometer.
- Challenges in Slag & Dross Environments
Scenario: Temperature measurement at the furnace sidewall or casting distribution trough Often, the aluminum surface is partially obstructed by dross balls or slag. AST suggests:
- Pick-Peak Mode: Capture the highest temperature when the metal surface is briefly visible
- Emissivity Monitoring: Use ε values to detect surface cleanliness
- Alarms: Configure alerts when emissivity drops due to slag buildup
- Shielding: Install light barriers to block external reflections that could interfere with readings
Even when full visibility isn’t available, pyrometers like the A5-IN can still provide meaningful data using strategic settings and modes.
Watch- Temperature Measurement Molten Casting
Molten & Solid Metal Measurement with A5-EX Infrared Pyrometer
Measuring Temperature of Moving Aluminum Ingots During Casting – A5-IN Pyrometer Application
Molten Aluminum Casting – Accurate Infrared Temperature Measurement with Pyrometer
Temperature Measurement in the Aluminum Melting and Casting Process
Conclusion: Optimizing Your Casting Line
Effective temperature monitoring in aluminum melting and casting hinges on:
- Choosing the right pyrometer model and spectral range
- Calibrating for both solid and molten phases
- Setting optimal reaction time for moving ingots
- Dealing intelligently with visual obstructions and reflections
Accurate Sensors Technologies delivers advanced infrared pyrometry solutions that adapt to real-world foundry challenges—enhancing quality, safety, and control.